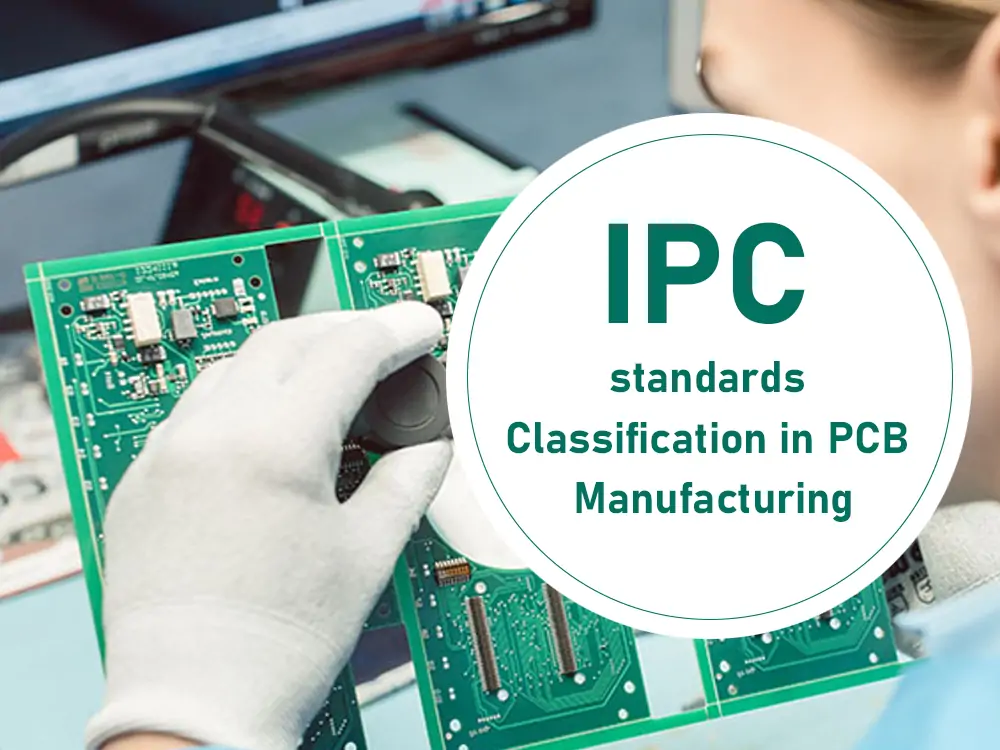
Introducción
IPC Class or IPC standards are often stated when making electronic products. These include Printed Circuit Boards (PCBs) and Printed Circuit Board Assemblies (PCBAs). Have you ever wondered what these are?
It’s essential to meet specific IPC standards for each product type produced. These standards also categorize electronic products into IPC Classes (1, 2 and 3).
What exactly do these IPC classes mean, and what are their differences? What IPC standards govern the PCB production process?
Keep reading to get insight into various aspects of IPC classes and standards.
What Is IPC?
IPC is a global association. It sets standards for the assembly and production requirements of electronic products. It helps companies build better electronic products. It’s accomplished via established standards, education, certifications, leadership, and advanced solutions.
Today, IPC standards enclose each PCB design process, production, assembly, testing, and approval. They have become common in the electronics manufacturing industry.
Brief History and Current Position
IPC stands for “Institute of Printed Circuits.” It was founded in 1957 by 6 PCB manufacturers as an association, and later, more companies joined the association.
In 1999, the association was renamed Association Connecting Electronics Industries. But it still uses the short form IPC.
Today, more than 4000 companies are part of the association.
Why Implement IPC Standards?
IPC provides several standards to ensure that you make excellent and reliable Printed Circuit Boards.
To achieve this, you must incorporate quality in the production process. It must be supported with continuous attention to detail and zeal for quality.
These are some important reasons why implementing IPC standards is necessary:
1. Enhance electronic products’ reliability and quality
IPC standards help electronic manufacturing services companies improve the quality and reliability of their varied products. Therefore, it’s necessary to adhere to IPC standards throughout the production process.
It also reduces the failure risk of electronic products and increases their lifespan.
2. Aid in managing and controlling production costs
Using IPC standards helps companies to integrate PCB design and manufacturing. Thus, this can aid in reducing and controlling production costs.
3. Helps companies provide customized and uniform training programs
IPC standards assist companies in providing customized uniform training programs like product development. The motive is to improve the skills and abilities of each employee. It also assists them in being aware of the objectives of the production process.
4. Enhance communication
IPC standards are used by electronic manufacturing services (EMS) providers along with customers. It ensures that they speak the language of the worldwide electronics industry. They can range from designers to assemblers.
Here, everyone is using the same terms and aware of the expectations. Thus, it enhances communication. The outcome is happy customers who are satisfied with the production process and product quality.
5. Improve reputation
IPC standards improve the quality of your products. It leads to the improvement in your reputation as a company. It also results in new opportunities.
Thus, you’ll be able to take over the competitors and increase customer satisfaction. It will also enhance the profitability of your company.
What IPC Standards Are In Place For The PCB Production Process?
There are numerous IPC standards for each stage of the PCB production process. PCB manufacturers must follow these standards. Here are a few examples of some standards to give you an idea of them:
1. IPC-2581
IPC-2581 is a common standard. It deals with sending information between a PCB designer and a producer or assembly company. It’s a source of standard format helping to exchange design data for steady production outcomes.
2. IPC 2221
IPC 2221 is a common standard for Printed Circuit Board design. It’s the most widely used in the IPC 2220 design standard series.
This series covers specifications for particular PCBs, such as flex, rigid, and MCM-L. It also covers parts lists, design layouts, materials, electrical properties, etc.
3. IPC 4101:
IPC 4101 standard applies to requirements of base materials (substrate). These materials are commonly known as prepreg or laminate. This standard is mainly used for multilayer or rigid boards.
This standard deals with the materials used and their properties.
4. IPC-A-610
This standard is famously known as the Acceptability of Electronic Assemblies. It establishes the principles for the acceptance of final products.
5. IPC-6011
The IPC-6011 standard caters to general requirements for Printed Circuit Boards. It establishes the reliability and quality levels Printed Circuit Boards should meet. These are for the design, assembly, testing, and assessment stages.
6. J-STD-001
IPC J-STD-001 is also an important standard. It outlines the materials, procedures, and other requirements for making the finest soldered interconnections. It covers process controls and provides requirements for varied electronic product types.
Grasping the IPC classes 1, 2 and 3
You got an overview of IPC standards earlier. IPC standards IPC A-600 and IPC A-610 outline the three IPC Classes: 1, 2, and 3.
IPC Class meaning
These classes are essential at each stage of PCB design, production, and assembly. The goal is to manufacture quality products. It’s also about continuing a spirit of competency in each stage of the production process.
The IPC classes are appropriate to three types of electronic products related to PCBs. These are:
IPC Class 1: General Electronics Products
This class is the lowest and applies to products in the general electronics category. It consists of Printed Circuit Boards with the lowest quality needs. It is usually found in products with an anticipated short life cycle.
In other words, these products have simpler functions and a brief lifespan. These can include routine electronic products you can find at home. Some examples include:
- Standard headphones
- children’s toys
- coffee makers
- TV remote control
- Portable speakers
- LED lights
- Blenders
In short, manufacturers make IPC Class 1 products for daily use. Their failure has no major consequences other than replacing the product or causing inconvenience. The focus is on cost-efficient items that meet basic operational needs.
Also, the products of this class are not expected to withstand extreme conditions.
IPC Class 2: Dedicated Service Electronics
This category comprises all electronic devices needing a long life cycle and continual performance. It’s higher than IPC Class 1. It comprises products with PCBs that are more reliable and have longer life. Even though they are not highly critical, they operate constantly.
Electronic products in this class undergo strict standards while they are being made. The goal is to achieve a long lifespan.
Some examples include:
- Laptops
- Air conditioners
- Tablets
- Smartphones
- Microwaves
- Televisions
- Some mining equipment
- Routers and switches
- Medical devices in non-life support applications, e.g., diagnostic monitors.
You see that continual performance is desired for such devices but not critical.
IPC Class 3: High-Reliability Electronics
The IPC Class 3 category represents the highest quality and reliability of electronic products. It belongs to products that must work faultlessly under the most demanding and stringent conditions.
Failure is not a choice in such a class. It can result in disastrous outcomes, such as loss of life or considerable financial losses. Products of this class are highly critical and must ensure continuous operation. They are made to last and should not undergo any downtime.
IPC Class 3 PCB is inspected and tested at the maximum level. It’s according to the strictest of standards. That makes the products of class highly reliable. Each component and assembly process of products is manufactured and tested very precisely and carefully.
Some examples of the products in this class include:
- Defense and Military equipment
- Electronic monitoring system
- Life support medical systems like ventilators
- Aircraft avionics and controls
- Automobile PCB and other vital systems
What Other Important Electronics Industry Standards Are There?
Apart from IPC standards, there are also other important electronic industry standards. These are as follows:
1. ISO
ISO stands for International Organization for Standardization. The ISO standards apply to production and quality control in varied industries. Being an international standard type, it applies to the electronics industry as well.
Some common ISO standards relevant to the electronic industry are:
ISO 9000: Quality management certification
ISO 9001: Quality assurance certification
ISO 14001: Environmental management system certification
2. UL
UL is a worldwide testing and certification company. Established in 1894, it has published about 1800 quality, safety, and sustainability standards. These standards have become national standards in countries like the USA and Canada.
Some examples of UL standards include:
- UL 796-For Printed Circuit Boards
- UL 916-ForEnergy Management Equipment
3. RoHS
RoHS stands for Restriction of Hazardous Substances. It’s an obligatory standard under a directive in the European Union. This standard was put into place on 1st July 2006.
It regulates the use of specific unsafe substances in Electrical and Electronic Equipment (EEE).
The motive behind this standard is to protect the environment and human health. It’s about decreasing the quantity of dangerous waste produced by electronic products. The goal is also to make their manufacturing safer.
Discovering the Difference Between IPC Class 2 and Class 3
We examined IPC Class 1, Class 2, and Class 3 earlier. The following table compares the two most notable IPC Classes (Class 2 and Class 3). These are according to varying factors:
Factor | IPC Class 2 | IPC Class 3 |
Categoría | Dedicated service electronics | High-reliability electronics |
Quality | Bien | Made to last without failure or malfunction |
Lifespan | Long | Very long |
Examples | Laptops, smartphones, routers and switches, televisions, microwave ovens, printers and monitors | Life support medical equipment (like pacemakers and ventilators), aerospace electronics, military electronic systems, electronic systems monitoring power and nuclear plants |
Materials and Components | The materials and components in electronic products are of high quality. | The materials and components in electronic products are of the highest quality. |
Testing and Quality control | IPC Class 2 electronics undergo significant testing and quality assurance checks. | Each unit in IPC Class 3 electronics undergoes more thorough and rigorous testing and quality assurance checks. |
Support and warranty | The products have long IPC PCB standards support and warranty along with improved customer support. | The products have extensive support and warranty after sale, along with regular updates. It ensures continuous performance. |
PCB Design and Manufacturing | IPC Class 2 PCBs have worthwhile production tolerances but are less strict. | IPC Class 3 PCBs have the most stringent production tolerances. It ensures the highest reliability and preciseness. |
PCB Inspection | PCB Inspection is less thorough | PCB inspection is more thorough |
Asamblea del PWB | Must follow strict guidelines about component placement; cleanliness is less thorough. | They must follow the strictest guidelines about component placement; cleanliness must be more thorough. |
Conclusión
By now, you know the definition of IPC Classes and their differences.
You also know about different IPC standards for the PCB production process. We also covered why implementing IPC standards is necessary.
Indeed, IPC standards and classes are paramount to the electronic manufacturing industry. They reveal the quality of each PCB type. They assure that the products are reliable in the long run.
Thus, your manufacturer must be qualified to work with you on these standards and classes.